Manufacturing Supply Chain Upsets
MATERIALS LABORATORY CASE STUDY 2
THE PROBLEM
A manufacturer noticed recent material provided by a supplier was not performing as well as what had been provided previously, and asked SI’s Materials Laboratory to investigate.
THE SOLUTION
Two pieces of stock material were submitted for analysis (Figure 1). The sample marked as F was the most recent material supplied to a manufacturer and the unmarked sample was the material that had been previously supplied. The newer material was not performing as expected and SI was asked to compare the two samples to identify any differences.
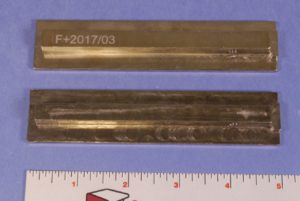
Figure 1. The submitted samples of material
Cross sections were removed from both samples and prepared for metallographic examination. The microstructures from each are shown in Figure 2. The newer material (sample marked “F”) had a microstructure consisting of pearlite in a ferrite matrix. The previously manufacturer supplied material had a microstructure consisting of Widmanstätten ferrite and bainite. Hardness measurements were made on each prepared sample. The F sample had an average hardness of 66.7 Rockwell B and the unmarked sample had an average hardness of 90 Rockwell B. The measured hardness values were consistent with the observed microstructures.
The pearlitic microstructure and lower hardness value indicate that the newer material would have a lower tensile strength than the older material, which was likely the reason it was not performing as expected in its final application. Armed with this information the manufacturer has the information necessary to resolve the issue with the supplier.
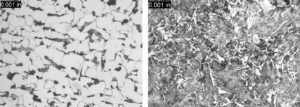
Figure 2. The typical microstructures from the marked sample (left) and the unmarked sample (right)
TEST METHOD DETAIL
Metallographic examination involves mounting the cross-section, then grinding, polishing and etching. In this case, the carbon steel material was etched with a 2% Nital solution. The prepared sample was examined using an optical metallurgical microscope for examination at magnifications up to 1000X. The images shown were originally taken at 500X.
RELATED MATERIALS