News and Views, Volume 55 | Digital Twins – Concept, Uses, and Adoption in Industry
/in Abbas Emami-Naeini, Company News, Dick de Rover, Fossil Power, News and Views, Nuclear Asset Integrity, Sarbajit Ghosal/by Structural IntegrityBy: Sarbajit Ghosal, Dick de Rover, and Abbas Emami-Naeini
Digital Twins are dynamically synchronized digital representations of physical equipment or systems. This technology is emerging in the power generation industry and assists with early detection of potential failures, failure accommodation, optimized maintenance schedules, development of next-generation equipment, and workforce training.
SC Solutions has decades of experience with technology that powers devices in your pocket and on your desk and continues to be an industry leader in providing process control solutions to the semiconductor industry. SI Solutions brings together the combination of SC’s controls expertise with that of Structural Integrity’s, modeling expertise and highly capable AIMS platform cyberinfrastructure, cultivating the total package to handle the development of digital twins in critical infrastructure.
Origin of the Digital Twin Concept
On April 13, 1970, while 210,000 miles from Earth, the three astronauts in Apollo 13 were startled by a loud bang that shook their tiny spacecraft. Astronaut John Swigert immediately messaged the NASA Mission Control Center: “Houston, we’ve had a problem here.” One of the two oxygen tanks had exploded catastrophically, damaging the other tank and thus putting the astronauts in extreme danger. The mission had to be aborted.
NASA engineers and scientists in Houston worked feverishly around the clock to devise a way to bring the astronauts back safely. They were assisted by 15 simulators used to train astronauts and mission controllers in every aspect of the mission, including multiple failure scenarios [1]. These simulators, made up of high-fidelity models, had been developed at NASA in the 1960s as “living models” of the mission [2]. They were controlled by several networked computers, e.g., four computers for the command module simulator and three for the lunar module simulator [1]. By utilizing these simulators and real-time sensor data from the spacecraft, Mission Control devised a successful strategy to guide the astronauts back to Earth safely.
While the term “digital twin” was coined later, the Apollo 13 mission is widely recognized as the first application of this technology, where a digital version of a physical system was updated with sensor data which was then used to run simulations to test potential solutions to troubleshoot a complex, high-stakes problem in real-time.
What Exactly is a Digital Twin?
Claims of using digital twins to solve various problems and marketing supposed digital twin products have proliferated over the past seven years. The term’s use to describe virtual representations of all sorts of assets, ranging from cities to racing cars, has led to considerable confusion. Experts from academia, industry, government agencies, and standards organizations have published definitions describing the key features of digital twins to mitigate confusion [3]-[5].
Since the definition often gets bogged down in semantics, it is preferable to identify the three primary parts that constitute a digital twin (DT). They are the physical object or process and its physical environment, the digital representation of this object or process, and the communication channel between these two that helps maintain state concurrence of the digital representation even as the state of the object or process changes dynamically. This communication channel transmits sensor data and state information and is called the digital thread. It is noted that a static model of a system or process cannot be a DT. A dynamic model whose parameters are not updated to reflect changes in the physical counterpart of the model also cannot be a DT.
The International Organization for Standardization (ISO) adopted a concise yet complete definition of a digital twin in 2021. The standards document on the digital twin framework for manufacturing (ISO 23247 [5]) defines a digital twin as a “fit-for-purpose digital representation of an observable manufacturing element with synchronization between the element and its digital representation” [6].
Whether maximizing machine performance or preventive maintenance, a clear goal for the twin is necessary for selecting the states of interest and a corresponding model of sufficient fidelity.
A digital twin of the next-generation machine, a digital twin prototype (DTP), incorporates its physical twin’s design specifications and engineering requirements. The DTP is valid in the design phase before investing resources to build a hardware prototype. DTP simulations help designers decide whether the eventual prototype would meet performance specifications. Once the prototype is fabricated and operational, the corresponding DT, now updated with sensor data, is called the digital twin instance (DTI). A collection of DTIs with a standard function is called a digital twin aggregate (DTA). DTA’s may be a collection of digital twins of the same equipment, e.g., several nominally identical pumps in a hydroelectric power station, or different equipment with a common purpose, e.g., robots, conveyors, and quality inspection stations in a material handling system of a factory.
Additionally, a simulation with a DT does not necessarily have to be performed in real-time—it would depend on the application. A DT used for real-time system control must run faster than real time. However, a high-fidelity DT used for design optimization may run simulations over many hours to sufficiently probe the parameter space in its underlying models.
Figure 1. Digital twin (DT) of a power generation equipment operating in parallel with its physical twin.
DTs have three key aspects: model, data, and services, i.e., services used or provided by DTs. The software that makes up the DT of a system has different functionalities that address these three aspects. We have divided the software into six broad classes:
Six Classes of Software used in a Digital Twin System
Software implementation of models: These may be physics-based models or gray box models (a combination of physical subsystem models and input-output heuristic models) of the physical components that may be integrated to create the system DT. The physics-based models are low-order versions of complex finite-element models that run simulations faster than in real-time. The gray box models combine known physical/mathematical relationships (the system model – the “white box” part) with phenomenological relationships or black-box models such as artificial intelligence/machine learning (AI/ML) that replace physics too complex to be modeled or overlooked. One example of gray box models is surrogate models such as Gaussian process models and physics-informed machine learning (PIML).
Sensor data-related software: This group includes software for signal processing and noise filtering of the sensor data. The data acquisition frequency may vary from milliseconds for real-time sensor data to hours for statistically sampled measurements of attributes of a manufactured product. Depending on the number of sensors and sampling rate, the volume of data may be substantial, especially in a manufacturing application. There is also software for interacting with external databases that would organize and store the data, make them available for updating the DT, and help perform prognostic tasks. This class of software would also include the implementation of sensor fusion algorithms and data compression algorithms.
Analytical and prognostic software: This class of software provides the DT’s “intelligence” and its benefits to the user. It includes the implementation of predictive maintenance algorithms, system performance optimization, decision support, and anomaly detection. Also included is software for updating models with sensor data by estimating new model parameters or re-training machine learning networks.
Software that enables user interaction: A well-designed user interface is key to digital twins gaining wider acceptance. A DT should include tools for customizing dashboards and interactive control interfaces, 3D graphics libraries for visualization of the physical twin at different levels of detail, and reporting tools for its prognostic and related functions. Some DTs may benefit from using augmented reality/virtual reality (AR/VR) tools.
Network communication and security software: This software is part of the so-called “digital thread” that involves all aspects of securely dealing with data streaming from hundreds, if not thousands, of sensors. Tasks performed by such software would include message queuing, protocol translation, connection monitoring, API management, and, very importantly, network security. For DTs to gain trust, the intellectual property (IP) embedded in the DT and in the data must be protected against all cyber threats.
Administrative software: This group includes “everything else”! It provides software and tools for configuration and change management, requirements tracking, documentation, access control, resource monitoring, and backup.
Drivers for Digital Twin Development
The confluence of advances in four technological factors has driven the development and adoption of digital twin technology over the past decade. These factors are:
- The decreasing cost of high-performance computing (HPC), both at the edge (i.e., in physical proximity to the end-user or the physical twin) and in the cloud. While problematic limitations imposed by physics and manufacturing costs have slowed Moore’s Law, computational power has continued to increase through a combination of heterogeneous integrated circuit (IC) architecture, such as 3D stacking and chiplets, and chips designed for a specific use, such as graphics processing units (GPUs).
- The proliferation of sensors and sensor networks (sometimes called the Internet of Things or IoT) enables individual sensors to acquire, flow and store data. Data analysis makes it possible to monitor a variety of system attributes, which, in turn, allows the digital twin to keep up with changes occurring in its physical twin.
- Availability of software tools enabling faster development of more complex models. Modeling techniques have been developed to use different models, including physics-based, data-driven, and machine learning (ML) models, to create a more comprehensive and accurate digital representation of the physical system. Merging various modeling approaches helps capture a more precise view of the physical system by leveraging the strengths of each model type. Commercial modeling software such as ANSYS also provides tools to develop surrogate models, proxies for high-fidelity physics-based models, and speed up model simulations [7].
- The arrival of large language models (LLMs) developed in the field of generative artificial intelligence. Before the release of ChatGPT to the public in November 2022, the role of AI in digital twins was primarily in using supervised machine learning for surrogate and data-based models. LLMs have advanced “embedding” capabilities, i.e., they can significantly compress data (both numeric and text) while retaining essential information. For example, in a manufacturing setting, LLMs can organize data from maintenance logs, equipment images, and operational videos and make them available in a DT. Maintenance logs often have valuable information related to system failure diagnostics and health maintenance that would add to the DT’s capabilities. AI is expected to play an essential role in the future of digital twin technology.
The fast-paced progress made in the above technologies makes it possible to transform digital twins of complex systems from merely a nebulous concept to a valuable technology that can be implemented once a few hurdles (such as standardization and data sharing) are overcome. Figure 2 attempts to show how the digital twin concept has evolved from solid models and offline computations to the virtual representations of complex systems being developed.
Figure 2. Factors in the evolution of digital twins.
How Can Digital Twins Be Useful?
The holy grail of digital twin technology derives from its ability to monitor the health of its physical twin, and the benefits include the following:
Early detection of potential failures: While sensors in the physical twin can monitor the system’s local state in the proximity of the sensors, the digital twin’s states act as virtual sensors and effectively scan the state of the entire system and can detect anomalous behavior. When the DT incorporates reliable degradation models (e.g., heater degradation or crack propagation), it can predict potential failures. The process cycle may then be ended in an orderly manner to repair or replace the part without any damage to the system that may result from a catastrophic failure of the part.
Failure detection and accommodation: The digital twin can be a valuable tool in case of a component failure in equipment. There are different ways to perform such root cause analysis. One way is to use physically meaningful model parameters continually monitored by sensor data estimation. If a parameter value strays outside a specified range, the failure is related to the component associated with that parameter. A second method uses a bank of Kalman filters to detect anomalies. The second article in this series will examine failure detection for sensor and actuator failures in a rapid thermal processing (RTP) system in greater detail.
As an example of using DT for failure accommodation, if a temperature sensor fails in the RTP system, the DT’s estimate of the system’s temperature near the sensor (one of the DT’s states) can temporarily serve as a virtual sensor. The process can continue until the faulty sensor is replaced during regular maintenance.
Optimizing maintenance schedules: Currently, scheduled maintenance of equipment is more frequent than needed to avoid unplanned downtime. The ability to foresee some potential problems down the road allows a factory to implement predictive maintenance strategies to reduce cost by eliminating unnecessary maintenance.
Develop Next-Generation Equipment: The digital twin of an existing asset may be modified to help speed up the development of next-generation equipment. Simulations run with the latter are very helpful in determining whether the design would meet the desired performance goals. Design changes are fast and inexpensive to implement and test in virtual space, and they can help ensure that the prototype built would meet all the requirements. SC has used this approach with its equipment models, which are components of the equipment DT, to help its customers design and build next-generation equipment.
Workforce Training: Since the roots of digital twins go back to NASA’s simulators for training astronauts, it is not surprising that DTs are finding a role in the education and training of the industrial workforce. Here, DTs can provide an immersive learning experience and practice with virtual control of tools to run real-time simulations, often aided by virtual reality accessories. Like other digital educational tools, DTs have the advantage of offering customizable learning, distance learning, and a safe environment without any accidents resulting from incorrect operation. Finally, DTs can be used for scenario-based training dealing with various operational conditions, equipment failures, and emergency response training. While the prognostic applications of digital twins require very frequent updating with sensor data, the DTs for other applications need significantly less updating.
Potential Applications for Digital Twins in Power Generation and Other Critical Infrastructure
The digital twin paradigm offers promise in the energy industry where a DT is developed and maintained to identify changes in the system that helps detect anomalies, make maintenance decisions, or perform root cause analysis of failures. A finite element (FEM) model of a structure with a crack which is periodically updated with measurements of the crack dimension may be considered to be a DT of the structure whose purpose is to monitor crack propagation. One may scale up such models to larger structures, e.g., large components of energy systems such as gas turbines [8].
The application of DT technology to combined gas turbine, wind turbine, solar, and nuclear power plants are expected to increase in the years ahead with several application areas in the nuclear industry [9]. These include design, licensing, plant construction, training simulators, autonomous operation and control, failure and degradation prediction, physical protection modeling and simulation, and safety/reliability analyses [10].
SI’s expertise in FEM modeling, material degradation, and lifetime prediction models, together with the AIMS development team’s expertise in cyberinfrastructure, is well suited to building and maintaining a DT of an energy system or some other critical infrastructure and using the DT for preventive maintenance and other applications. DT is an evolving technology, and it may not be possible to fully automate the model updating process. Hence, the software as a service (SaaS) model may become the norm for DT products. SI is optimistic about the technical aspects of DT Technology and the opportunities to leverage these tools in supporting our clients.
Figure 3. Digital twin concept for a nuclear power plant [10]
Power Gen Applications
With the emergence of Digital Twins in the power generation industry, our teams are able to use the synchronized digital representations of equipment to assist with early detection of potential failures, failure accommodation, optimized maintenance schedules, development of next-generation equipment, and workforce training.
Our staff are positioned to support digital twins’ development, coinciding with SI’s modeling expertise and highly capable AIMS platform cyberinfrastructure, cultivating the total package to handle any digital twins’ needs. The AIMS Digital Solutions platform is integral to our mission of providing the best-in-value, innovative, fully integrated asset lifecycle solutions. Digital products paired with our expertise in Engineering, inspections, and analytics help achieve a holistic asset management approach to our clients.
References
- S. Ferguson, Apollo 13: The First Digital Twin, April 14, 2020. Available at: https://blogs.sw.siemens.com/simcenter/apollo-13-the-first-digital-twin/
- B. D. Allen, Digital Twins and Living Models at NASA. Keynote presentation at ASME’s Digital Twin Summit, Langley, VA, November 3 2021 Available at: https://ntrs.nasa.gov/api/citations/20210023699/downloads/ASME%20Digital%20Twin%20Summit%20Keynote_final.pdf
- L. Wright and S. Davidson, “How to tell the difference between a model and a digital twin,” Adv. Model. and Simul. in Eng. Sci., 2020, 7:13.
- The Digital Twin, Ed. N. Crespi, A. T. Drobot and R. Minerva, Springer, 2023.
- ISO 23247-1: Automation Systems and Integration – Digital Twin Framework for Manufacturing – Part 1: Overview and general principles. International Organization for Standardization, Geneva, Switzerland, 2021.
- G. Shao, S. Frechette, and V. Srinivasan, An Analysis of the New ISO 23247 Series of Standards on Digital Twin Framework for Manufacturing, Proc. of the ASME 2023 Manuf. Sci. Eng. Conf., MSEC2023, June 12-16, 2023, New Brunswick, NJ, USA.
- M. Adams, et al., “Hybrid Digital Twins: A Primer on Combining Physics-Based and Data Analytics Approaches,” in IEEE Software, vol. 39, no. 2, pp. 47-52, March-April 2022.
- D. de Roover, Possibilities and Challenges in Developing a Digital Twin for Rapid Thermal Processing (RTP), APCSM Conference, Toronto, Canada, 2024.
- N. V. Zorchenko, et al., Technologies Used by General Electric to Create Digital Twins for Energy Industry. Power Technol. Eng., 58, 521–526, 2024.
- U.S. NRC, Digital Twins. Available at: https://www.nrc.gov/reactors/power/digital-twins.html#reports
News and Views, Volume 55 | Nonintrusive and Robotic Solutions for Tank Asset Management
/in Company News, Jason Van Velsor, News and Views, Non-Destructive Evaluation/by Structural IntegrityBy: Jason Van Velsor
Nuclear plant aging management programs require periodic inspections of liquid storage tanks. Traditional inspection methods can be disruptive, requiring tanks to be drained to provide personnel access. SI has developed innovative solutions, including screening techniques that can identify degradation from the tank exterior, and submersible robotics that perform comprehensive NDE without draining. Although initially developed for nuclear applications, these technologies can be employed at conventional power generation, petrochemical, and municipal utility facilities.
Nuclear Industry Guidelines
The nuclear industry established guidelines for integrity management of underground piping and tanks in the early 2000s with the publication of NEI 09-14. More recently, additional constraints have been imposed for plants pursuing life extension, especially for sites applying for subsequent license renewal (SLR) to extend permitted operation from 60 to 80 years. These new requirements for outdoor and large atmospheric tanks are conveyed in the form of specific guidelines for aging management programs (AMPs) within NUREG-1801, Revision 2 and NUREG-2191, Revision 1.
The guidelines within the NUREG documents apply to:
- All metallic outdoor tanks constructed on soil or concrete.
- Indoor metallic storage tanks with capacities greater than 100,000 gallons, designed for internal pressures approximating atmospheric conditions, and exposed internally to water.
- Other indoor metallic tanks that sit on, or are embedded in, concrete, where plant-specific operating experience reveals that the tank bottom (or sides for embedded tanks) to concrete interface is periodically exposed to moisture.
- For utilities with tanks meeting the above criteria, license renewal commitments generally necessitate performing examinations under one of the following three categories:
- Inspection of the bottom 20% of walls for wall loss and cracking.
- Inspection of the outer two feet of the floor plates for pitting/cracking.
- 100% inspection of the bottom floor plates.
Conducting floor inspections using traditional approaches that require draining and personnel entrance into the tank can be undesirable, given the potential impact on operations, as well as the possibility for certain tanks to contain radiological content. For this reason, many utilities have begun pursuing alternative solutions to safely and accurately perform tank inspections.
Traditional Approaches
Historically, utilities have emptied and entered tanks to conduct manual floor inspections. The scope of these examinations can range anywhere from visual to full volumetric inspection of the tank floor using electromagnetic or ultrasonic techniques. More recently, utilities have attempted to utilize robotically deployed examination methods to avoid emptying and entering tanks. Obtaining large-area NDE coverage of tank floors with robotic methods has usually fallen into one of two categories:
- Relatively simple robotic systems that deploy traditional NDE sensors for localized measurements, which may take an impractical amount of time to reliably obtain the required coverage, or…
- Relatively complex robotic systems that deploy a large quantity of traditional NDE sensors to obtain the required coverage more quickly, but that are large, complex, and often expensive to deploy.
Deploying any robotics in tanks is a challenging endeavor, with many practical factors that affect the ease and success of implementation. Several of these factors include:
- Accessibility – there are limited access points to the inside of a tank; they are often on top of the tank, and just large enough for a person to fit through.
- Visibility – maneuvering within a liquid-filled tank often relies on optical methods, which are impaired or even ineffective in murky or opaque liquid.
- Navigation – with poor visibility, continuously tracking the position of a robot within a tank (and hence, the location of acquired data) can be unreliable.
- Cleanliness – sediment present in the tank can impair data acquisition and cause additional visibility issues if agitated by the robot.
- Geometry – getting complete coverage at the tank edges and around internal features can be challenging or impossible given the size and limited maneuverability of some robotic systems.
- Tank Size / Inspection Time – for large tanks, obtaining complete coverage of all in-scope surfaces may require extended scanning time, which can impact operations and delay return to service.
- Liners/Coatings – tanks that have been lined with thick coatings such as fiberglass or carbon wrap can render traditional NDE methods useless.
Figure 1. GWPA from Tank Chime
SI’s Approach
SI offers a suite of engineering and inspection solutions that are designed to help our clients meet their examination commitments while minimizing the associated cost, time, and impact to operations. We work with our clients to determine the required scope of any necessary examinations, based on their Aging Management Program and license renewal commitments, and present a customized inspection approach. Where possible, inspection solutions that can be conducted from outside of the tank are prioritized over approaches that require deploying equipment in the tank. These approaches may include performing pulsed eddy current testing to examine tank walls through insulation or employing guided wave phased array (GWPA) from the tank chime plate to examine the outer annulus of the tank floor (Figure 1).
In situations where putting equipment inside the tank is unavoidable, SI has developed a robotic solution that uses a novel technological approach to provide rapid, 100% volumetric coverage with a range of NDE sensors deployed on a relatively basic robotic platform. Rapid, large-area volumetric coverage is obtained by mapping the tank floor with GWPA testing to identify critical areas (Figure 2). These critical areas can then be investigated using high-resolution, non-contact methods, such as electromagnetic acoustic transducers (EMATs) for UT thickness measurements or SI’s dynamic pulsed eddy current technology, SIPEC™, for dirty or lined tanks.
Figure 2. GW Phased Array Tank Floor Inspection
From a deployment perspective, SI’s robotic system is designed to fit through existing tank access points, can scale carbon steel walls, and can quickly switch between a range of sensor types. Additionally, SI has incorporated a proprietary acoustic vehicle positioning system, where sound pulses track the absolute position of the robot at all times, ensuring precision results and the ability to accurately relocate and rescan specific areas for follow-up activities or future inspections. The acoustic positioning system uses a transmitter placed on the robot and a series of receivers placed on the exterior tank wall to track the movement of the robot. With this approach, positioning is not reliant on visual or other optical methods that can be confounded by cloudy, murky, or otherwise opaque liquid and is not subject to encoder error or drift.
Engineering Support Services
Beyond inspection, SI provides integrated engineering support that couples directly with tank inspections. SI’s expertise includes disposition of findings, detailed evaluation of any anomalies, and optional integration with our piping and tank asset management database, MAPPro™. SI engineers are adept at employing detailed FEA models and/or fracture mechanics techniques to assess the acceptability of any observed flaws/defects. For time-critical inspections, engineering handbooks can be developed before the examinations to provide real-time disposition of any findings. Loading inspection results into MAPPro enables risk-ranking utilizing time-proven algorithms, thereby informing future programmatic actions.
Using the advanced deployment and inspection technologies highlighted herein, SI is able to comprehensively inspect and disposition findings from tanks of various sizes while reducing schedule risk and ensuring accurate results.
Tank Inspection NDE Technologies
- Guided Wave Phased Array (GWPA)
- Used to rapidly inspect large areas such as a tank floor.
- Provides 100% volumetric coverage in a minimal amount of time and with minimal surface preparation.
- Identifies critical areas that should be investigated further using more precise examination technology. This follow-up is completed by switching probe heads and conducting targeted quantitative exams.
- Can also be applied from the chime plate on the tank exterior to examine the outer annulus of the tank floor.
- Electromagnetic Acoustic Transducer (EMAT) Ultrasonic Thickness Testing
- A non-contact (up to 0.25 inches of liftoff) volumetric examination that provides quantitative wall thickness for either carbon or stainless-steel tanks.
- Electromagnetic sensors generate UT for thickness measurements and are electromagnetically coupled, thus eliminating the need for couplant or close contact with the test surface.
- This type of testing is helpful for corrosion mapping where surface prep is not possible or costly or if there is a coating/liner present; additionally, it allows for remote robotic inspections, including those where the probe is submerged.
- SIPEC™ Electromagnetic Thickness Testing
- Proprietary non-contact volumetric examination that works through internal liners and sediment (up to several inches) targeting either carbon or stainless steel.
- Employs a proprietary dynamic pulsed eddy current measurement technique for rapid scanning.
- Higher liftoff, lower resolution option when compared to EMAT UT.
News and Views, Volume 55 | Materials Lab Featured Damage Mechanism
/in Company News, Materials Laboratory, News and Views, Wendy Weiss/by Structural IntegrityCREEP FATIGUE IN STEAM COOLED BOILER AND HRSG TUBES
By: Wendy Weiss
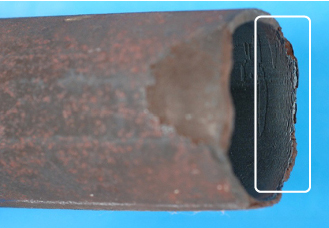
Figure 1. Tube to header weld crack.
Creep-fatigue is caused by the accumulation of damage through synergistic interaction of cyclic stress and elevated operating temperature. The creep and fatigue components of the damage usually occur at different periods in the thermal cycle to result in a failure with characteristics of both mechanisms. Structural Integrity has an experienced group of materials specialists and a full-service metallurgical testing laboratory that can help with any situation involving material property characterization.
Creep-fatigue is generally assumed to be the active mechanism when the rate of fatigue damage is influenced by the strain rate and hold times while the tube is operating at temperatures within its creep regime.
Mechanism
Creep-fatigue is essentially the accumulation of damage through synergistic interaction of cyclic stress and an elevated operating temperature. The creep and fatigue components of the damage usually occur at different periods in the thermal cycle. Cyclic loading may occur at temperatures within the material’s creep regime (≥800°F for Cr-Mo tubing). Once steady state conditions are reached, the component may continue to be exposed to high temperatures and localized stresses, which can result in the accumulation of additional plastic strains due to creep. Furthermore, if residual stresses due to thermal transients were present, creep relaxation would add to the magnitude of the inelastic strain. The key takeaway regarding creep-fatigue damage is that the fatigue life can be significantly less than would be predicted from pure fatigue test data.
Figure 2. Crack surface of the tube to header weld crack, with a thick oxide layer and creep damage along its length.
Typical Locations
- Superheater and reheater tubes where tube metal temperatures are in the creep regime
- Welded connections
- Bends
- Tube-to-header attachments
Features
- Generally initiates on the OD surface
- Typically, single cracks
- Cracks are generally relatively straight, relatively wide, and oxide-filled or oxide-lined
- Creep voids and microfissures can surround the primary crack, but creep damage does not have to be present
Root Causes
Creep-fatigue is caused by the interaction of stresses, both cyclic and static, and elevated temperature exposure. Root causes can include excessive stresses/strains, excessive tube temperatures, and unit operation.
Excessive stresses/strains can result from the following, many of which are related to HRSG operation: constrained thermal expansion, pressure changes, fluid temperature changes, non-uniform temperatures, load transfer between hot and cold conditions, changes in external loads, transient temperature differences, steam or water hammer, forced vibration, flue gas flow problems, thermal transients due to condensate flashing into tube circuits, improper attemperation, and incorrect or inadequate drains.
Excessive tube temperatures can result from excessive temperature ramp rates, poor distribution of tube temperatures, poorly designed thickness transitions at header connections and supports, and poor material selection for tubing.
The number of service hours, number of stop/starts, and the characteristics of the stop/starts are unit operation influences that can affect creep-fatigue damage.
Visit Our Metallurgical Laboratory Services Page
SEE THESE OTHER RELATED MATERIALS FROM THE SIA METALLURGICAL LABORATORY
Featured Articles
Case Studies
Metallurgical Laboratory Product & Services Information
News and Views, Volume 55 | Replacement of Large Equipment in Nuclear Power Plants
/in Company News, Dan Parker, Julio Garcia, Lachezar Handzhiyski, Natalie Doulgerakis, News and Views, Nuclear Asset Integrity, Nuclear Energy, Structural Assessments/by Structural IntegrityBy: Julio Garcia, PhD, PE, Natalie Doulgerakis, PE, SE, Dan Parker, PE and Lachezar Handzhiyski
With many U.S. nuclear plants having extended operation well beyond their original licensed life, it is necessary to replace certain critical process components (e.g., large pumps, turbine rotors, heat exchangers). In many cases, equipment manufacturers are asked to provide larger, heavier equipment to deliver higher output and improve efficiency. Prior to installation, the existing structure must be evaluated for the larger static loads as well as one-time loads applied during movement (transit and rigging). SI has successfully collaborated with owners, design engineers, equipment manufacturers, and installation contractors to ensure safety and minimize disruption during this process.
The U.S. power grid continues to benefit from the extended operation of traditional nuclear power plants, most of which began operation between 40 and 55 years ago. Due to unprecedented market demand, many plant owners are actively pursuing extended operating licenses (subsequent license renewal or SLR), and increased thermal and electrical power output (extended power uprate or EPU). Whether due to normal aging or increased performance demands, many plants are facing the challenge of replacing large pieces of original equipment (e.g., pumps, turbine rotors, heat exchangers) embedded deep within the facility. In many cases, sites are requiring larger and heavier replacement equipment to provide improved efficiency or additional margin.
THE CHALLENGE
Frequently, the initial structural design of these facilities typically did not explicitly account for replacement of certain large equipment (e.g., feedwater heaters, moisture separators, etc.). The removal, hauling, sliding, jacking, and installation of replacement equipment are new tasks that introduce significant operational and structural demands on the building structures as well as challenges to plant staff. High-demand loads may be temporarily imparted to building structures that were optimized during their original design based on original equipment and operations loads with limited strength margins. Re-evaluation of the building structure under the new, larger service loads is required, typically including gravity, seismic, wind, piping, and thermal loads. Particularly challenging and sometimes overlooked are new thermal loads imposed on the gravity load-resisting system of the building. These loads are the result of thermal deformations within the equipment piece itself or within other mechanical attachments, such as piping system that connects to it. Rigorous analyses are performed where there are complex networks of such attachments. Where multiple attachments connect to an equipment piece, it is key to combine the loadings at each attachment location in a conservative, yet realistic manner, to safely demonstrate structural adequacy.
SI has a proven track record of overcoming these challenges by applying rigorous structural analysis, optimizing retrofit strategies, and leveraging multi-disciplinary collaboration to limit disruption and minimize costs.
SI’S ROLE
Structural Integrity (SI) has provided key consulting services to support the replacement of large equipment for SLR and EPU, including moisture separator reheaters (MSRs) and feedwater heat exchangers (FWHs), among others. Working both as task leads, as well as independent reviewers, SI staff have successfully collaborated with owners, design engineers, equipment manufacturers, and installation contractors to safely replace large equipment. SI has provided key consulting related to technical and operational issues, helping to minimize disruption. Additionally, SI has provided a holistic approach that considers the benefits and challenges associated with use of different standards and methodologies to assess and potentially retrofit building structures designed and licensed many decades ago. As a result, SI structural engineers have been praised for providing significant contributions to optimize the process and minimize costs.
Figure 1. Operating Deck of a turbine building.
KEY SOFTWARE FOR STRUCTURAL ASSESSMENTS
Used for structural analysis and design, GTSTRUDL helps evaluate framing systems and load distribution under gravity, seismic, and equipment-induced forces.
A general-purpose structural analysis tool, SAP2000 assesses floor framing response to new equipment loads, ensuring existing structures can accommodate changes safely.
A high-fidelity FEA tool, ABAQUS models localized stress, thermal effects, and nonlinear interactions, providing detailed results in highly-stressed regions to maximize available structural margins.
PIPING ANALYSIS
Used to evaluate thermal, pressure, and mechanical loads applied to large stationary components, piping analysis software ensures system integrity and compliance with applicable codes (e.g., ASME B31.1). SI utilizes PIPESTRESS, AutoPIPE, and CEASAR II for these evaluations, depending on application needs and/or designer preferences.
PROJECT EXAMPLE 1 (1,158 MW 4-Loop PWR)
In support of the planned MSR replacement, SI developed 3-dimensional finite element models of the MSR units and their support frames, as well as the framing at the operating floor of the turbine building.
- Assessed combinations of pipe dead and thermal loads acting at MSR nozzle attachment locations to determine the most critical loading condition on the support frames and floor framing.
- Performed stress analysis of support frames to evaluate structural elements, welds, and bolted connections using ABAQUS.
- Performed structural evaluation of floor framing using SAP2000.
- Calculated framing member and connection capacities using the provisions of AISC 360 and ACI 318.
SI evaluated all structural elements within the MSR load path and confirmed the structure’s adequacy to resist the demands given the design loads provided by the plant staff. The result: SI’s recommendations and selected approach led to no structural retrofits being required of the turbine building, thus ensuring the planned operation was safe to perform while saving the unnecessary expense of reinforcing the structure.
PROJECT EXAMPLE 2 (1,220 MW 4-Loop PWR)
SI acted as the Owner’s engineer and performed an independent review of the MSR replacement project, including a review of the structural analysis of the turbine building under the installation and operation of the new and heavier MSRs, as well as the proposed structural retrofits.
- Independent review of the turbine building analysis methodology and numerical model in GTSTRUDL software.
- Review of loading and requirements data from design basis criteria, calculations, licensing commitments, manufacturer information and transport/hauling information.
- Verification of loading data in GTSTUDL model.
- Assessment of structural member capacity results from GTSTRUDL model.
- Performance of independent calculations for steel-reinforced concrete composite section capacities.
- Provided recommendations on the analysis methodology, loading data and applicable design standards to optimize the strength margins of the existing turbine building.
Through an independent review of the MSR replacement project, SI demonstrated unrealized structural margin, reduced the number of structural retrofits to support the heavier MSR units, and provided recommendations on licensing strategy for the review and approval of the structural modifications supporting the MSRs replacement.
Figure 2. Sliding and Replacement of a Moisture Separator Reheater.
News and Views, Volume 54 | Analysis of Ultrasonic Pipe Cleaning and Viability for Use in Nuclear Power Plants
/in Ashkan Nejad, Company News, News and Views, Vibration/by Structural IntegrityBy: Ashkan Nejad, Ph.D.
Ultrasonic cleaning is a non-destructive, low-cost technological method that uses high-frequency waves to remove contaminants from materials. The process utilizes specialized ultrasonic devices equipped with transducers that emit longitudinal and flexural waves at frequencies ranging from 15 kHz to 25 kHz to dislodge contaminants and carry them away with a cleaning solution. Cleaning pipes using this method, in accordance with regulation and safety standards, would safely and effectively reduce maintenance costs while ensuring optimal pipe functionality. When applied in the nuclear industry, this technique also allows for reduced contamination and radiation dose.
Structural Integrity has performed a study and multi-faceted analysis of this technique and its effect on pipe stresses caused by the induced vibrations to determine the feasibility of using ultrasonic vibration waveforms to clean internal piping in nuclear power plants.
FORCED FLEXURAL VIBRATION IN PIPES
The field of piping dynamics focuses on analyzing the stress caused by vibrations in pipes. This involves the use of established beam theories, such as Rayleigh and enhanced Timoshenko beam theories, which have been extensively studied. These theories are used to create piping dynamics models that assess the free vibration and bending stress within the pipe. However, in cases of forced vibration, the stress distribution on the pipe’s thickness due to external forces extends into three dimensions, while advanced beam theories can only model the flexural stress distribution in two dimensions. Although these theories are useful in analyzing pipe vibration responses in low-frequency vibration modes, they are inadequate for steady-state high-frequency harmonic loads on the pipe.
Experimental dynamic stress analysis is expensive and faces challenges when dealing with high-frequency flexural wavelength and instrumentation dimensions. Additionally, variations in pipe diameter and controlling voltage can significantly alter the dynamics of the ultrasonic resonator and pipe dimensions.
Despite these challenges, recent advancements in computational techniques and high-speed computers have made modeling elastic flexural wave propagation in piping systems more attainable. Accordingly, this study employs linear dynamics finite element (FE) analysis to simulate the flexural stress wave propagation in two ultrasonic resonator devices attached to a stainless-steel pipe. The subsequent extraction of three-dimensional stress and linearization stress distribution facilitates the evaluation of peak and bending stress as alternating stress. This analysis is then compared with the endurance limit, establishing a framework for qualifying the utilization of ultrasonic cleaning devices in nuclear plant piping systems.
STRESS LINEARIZATION
The Stress Linearization tool in the ANSYS program is used to separate stresses within a section into constant (membrane), linear (bending), and peak components. This option works by using a path defined by two nodes that traverse the thickness of the pipe cross-section. The path includes two endpoints, the coordinates of the cross-section (nodes), and 47 intermediate points automatically determined through linear interpolation in the active display coordinate system. Both start and end nodes are typically assumed to be located at free surfaces with the highest local equivalent stress intensity.
Figure 1. linearized stress distributions throughout the pipe thickness.
To calculate the membrane values of the stress components, an averaging integral is used across the thickness, with the centerline situated at the midpoint of the pipe thickness. Figure 1 shows the linearized stress distributions throughout the thickness, with the center of thickness as the coordinate center. The normalized bending stress can be compared with the allowable stress endurance defined in ASME OM3, but only for low-frequency modes where the bending stress is the dominant alternating stress. However, in high-frequency forced vibration, the stress distribution caused by shell-mode flexural waves through the thickness and longitudinal directions is approximately three-dimensional around the external force locations and two-dimensional far from the applied force location. This can make the peak alternating stress higher than the bending stress. Therefore, for comparison with allowable stress, peak stress should be considered as a conservative method. This approach ensures a comprehensive assessment of stress distribution and facilitates a nuanced analysis of constant and linear stress components within the specified section.
FORCED HARMONIC EXCITATION AND RESPONSE
When the ultrasonic resonator has voltage applied, with a frequency sweep from 21 to 22.5 kHz, this results in the harmonic displacement of the piezoelectric disks. The displacement then travels through the contacts between the ultrasonic cleaning component and the pipe. To analyze the equation of motion, the Harmonic Full Method is used. The Full Method involves solving a system of simultaneous equations directly using a Sparse matrix solver designed for complex arithmetic, Equation (1). This static complex form is derived from the forced equation of motion shown in Equation (2). The I and R subscripts in Equation (2) show the real and imaginary components of the complex vectors. The method accommodates various loads and boundary conditions. It also incorporates the effects of inertia and damping components to obtain the forced vibration displacement response. A conservative damping coefficient of 0.5% is used to simulate energy dissipation in the material through hysteretic damping. The calculated displacement is
The stress intensity is calculated, which is twice that of Shear Tresca. Afterward, it is linearized and compared with the allowable stress limitations. This methodology accurately assesses the resonator’s dynamic response and its implications on stress levels. It provides conservative insights into the structural performance under harmonic excitation.
SI’s RESULTS
SI conducted studies and analyses to find the benefits of using ultrasonic vibration waveforms to clean internal piping in nuclear power plants to enhance flow dynamics and reduce radiation exposure. The ASME Code for Operation and Maintenance of Nuclear Power Plants was followed to monitor pipe vibrations, and computational tools such as finite element analysis were utilized to assess piping responses to dynamic loads induced by ultrasonic transducers.
Figure 2. Displacement Harmonic response of pipe under high-frequency transducer loading through the Couplers.
Based on our findings, SI proposes a new approach that utilizes linearized stress intensity derived from finite element linear dynamics analysis tools. This approach offers a more conservative estimate of allowable alternating peak stress values compared to relying solely on bending stresses. This method addresses the limitations of linearized alternating bending stress in accurately calculating stress under high-frequency harmonic loads, where shear waves and shell modes are induced.
Our research confirms the efficacy of linearized peak stress as a superior metric for evaluating stress-induced fatigue in high-frequency ultrasonic cleaning applications.
News and Views, Volume 54 | Monticello Nuclear Generating Plant – BioShield Evaluation
/in Company News, Dan Denis, Livia Costa-Mello, News and Views, Nuclear Asset Integrity, Nuclear Energy, Shari Day/by Structural IntegrityBy: Livia Costa-Mello, Shari Day, and Dan Denis
Figure 1. Example of RPV and Bioshield showing areas of interest for evaluation.
Background
Many U.S. nuclear plants are completing license renewal (LR) activities to extend their operating life. The initial LR application extends operating licenses from 40 to 60 years; the subsequent renewal (SLR) further extends this from 60 to 80 years. As part of the LR/SLR application process, utilities must demonstrate that they have accounted for a variety of potential aging mechanisms that may take place over the ensuing operating period. One such mechanism is the loss of strength and/or ductility due to long-term exposure to high levels of radiation. This includes the reactor pressure vessel (RPV) and primary system piping but also extends to support structures (steel/concrete) in the vicinity of the RPV.
Xcel Energy submitted their SLR application for the Monticello Nuclear Generating Plant in January 2023. Constructed in the 1960s, Monticello is the oldest operating boiling water reactor (BWR) in the U.S. fleet and will reach 60 years of operation in 2030. As part of the Nuclear Regulatory Commission’s (NRC’s) standard review plan (SRP) for SLR applications1, detailed evaluations are recommended for steel and concrete structures which are predicted to exceed certain established thresholds of irradiation dose. This includes the biological shield wall (also referred to as the “bioshield” or “sacrificial shield”), a large concrete and steel structure that surrounds the RPV whose primary purpose is to shield workers and equipment from high levels of neutron and gamma radiation. In addition, the bioshield provides support for other critical components.
Xcel contracted SI to perform an evaluation of the Monticello bioshield in support of its SLR application. Initially, SI assessed embrittlement of the concrete and steel in accordance with the methodology in NUREG-15092 . Following questions posed by the NRC reviewers, additional clarifications were requested regarding plant-specific materials, justification of gamma heating parameters, and inclusion of weld residual stresses. SI performed separate heat transfer and fracture mechanics analyses to address these inquiries. This article summarizes the approach and results of this first-of-a-kind evaluation.
Figure 2. Typical Reduction in concrete strength due to irradiation.
Assessment of Bioshield Concrete Structure
As illustrated in figure 1, the portion of the shield wall that is critical for support purposes is near the bottom of the RPV, well below the active core. However, in accordance with the SRP, the concrete within this region is evaluated for irradiation-induced capacity reductions in accordance with methodology outlined within related EPRI reports. Both neutron and gamma dose were evaluated in accordance with NUREG-2192 guidelines, along with expected operating temperatures experienced by the concrete.
Radiation exposure levels for the Monticello bioshield at the end of the SLR operating period were computed via separate third-party analysis. The computed neutron fluence was less than the threshold for potential concrete damage, rendering it unnecessary to evaluate this item, but the computed gamma dose exceeded the potential damage threshold. Therefore, SI performed a detailed study to extrapolate the gamma exposure and any associated loss of strength for the load-bearing portion of the bioshield wall. The evaluation compared published lower-bound strength values from literary sources to the fluence values obtained from which a conservative factor on reduction in structural capacity was determined.
SI performed a detailed set of structural calculations to benchmark the original design basis analysis against the pertinent code of construction, ACI 318-63. These calculations were repeated for the predicted reduction in strength, and for all locations the predicted loads (or “demand”) were less than the available capacity. Thus, the structural portion of the bioshield wall was assessed to be acceptable for extended operation through the SLR period.
Figure 3. Dpa Variation as a function of Distance from Core Mid-Plane, Adjusted to Bounding Dpa for Shield Wall
Assessment of Bioshield Steel Liner
SI performed an assessment of the steel liner plates on either side of the bioshield wall, in accordance with NUREG-1509. The evaluation began with identifying the region of the bioshield subject to the highest radiation exposure. Comparing the elevation of the active core to the predicted distribution of neutron irradiation, the region of interest was determined to be ±100 inches above/below the core centerline. In this region, the only structural steel elements are the WF27x177 columns and the 1-¾” and ¼” thick liner plates.
For the indicated region, the effect of irradiation on the shift in ductile to brittle fracture transition temperature (known as “nil ductility temperature” or NDT) was evaluated. An NDT shift is calculated by referencing the irradiation at various elevations against criteria from NUREG-1509; this value is added to the initial NDT to compute an adjusted NDT.
ANSYS was used to develop a finite element model of key structural members for subsequent analyses. To benchmark the original design basis analysis, the model was initially developed using only the columns, girders, and stabilizers, after which all design basis loads were applied. However, the results from this model were observed to exhibit significant displacement of the steel columns due to weak axis bending. Therefore, SI developed an enhanced model for the key embrittled region to include the liner plates. The maximum principal stresses from this enhanced model were demonstrated to be less than the 6 ksi operational stress limit in NUREG-1509. Therefore, the steel portion of the Monticello bioshield was determined to remain structurally sound for the period of SLR extended operation.
Figure 4. Frame Model of Shield Wall Space Frame
Upon initial NRC review of the concrete and structural evaluations, additional questions were raised regarding NRC desired modifications to the NUREG-1509 methodology for extended SLR operation. The primary focus of these questions related to conservatism of the analyses when accounting for Monticello-specific properties, such as gamma heating of the concrete and impacts of weld residual stresses. Accordingly, SI developed a plant-specific heat transfer evaluation, and used those results to perform a fracture mechanics analysis of the stress state in the limiting beltline region.
Bioshield Heat Transfer Analysis
During NRC review of the steel and concrete analyses described in the prior sections, questions were raised regarding the potential for additional degradation of the concrete due to extended exposure to high temperatures and gamma-induced heating. To address these questions, SI developed a heat transfer model of the bioshield, accounting for RPV insulation, the annular air gap, and conduction through both liner plates and the concrete. Calculations were performed both by hand and using an axisymmetric model within Abaqus.
Figure 5. Detailed stress analysis results for critical region of bioshield.
The maximum temperature within the concrete portion of the bioshield was calculated to be below a 150 °F threshold value from the American Concrete Institute (ACI) for nuclear safety-related structures. The added temperature due to gamma radiation heating was estimated as less than 1.5 °F. Therefore, the bioshield was determined to be acceptable for long-term thermal exposure. The temperatures during operation do induce additional thermal expansion stresses in the hoop direction on the outer liner. Using the heat transfer model and application coefficients of expansion, these stresses were estimated to be less than 1 ksi, which are judged to be minimal given that primary loads on these members are in the bioshield-axial direction. Based on these results, there is no concern for thermally induced damage of the Monticello bioshield over the course of the SLR extended operating period.
Bioshield Fracture Mechanics Evaluation
NUREG-1509 includes an evaluation of a postulated flaw in structural steel members, in accordance with the fracture toughness approach in ASME Code, Section XI, Appendix G. For Monticello, the bioshield is constructed of ASME A36 steel, which was considered for computation of the NDT temperature, resulting in an allowable fracture toughness based on the ASME code. However, when considering industry literature and prior SLR evaluations, this value was conservatively reduced for the Monticello Evaluation. The fracture mechanics evaluation from NUREG-1509 was reproduced, using inputs from the steel liner FEA and bioshield heat transfer analysis. The resulting analysis demonstrated sufficient margin between the applied stress intensity and conservative allowable fracture toughness, confirming that the Monticello bioshield would remain intact with no potential for brittle fracture even in the event of a postulated flaw.
Figure 6. Simplified heat transfer model for bioshield.
Conclusions
SI completed a first-of-a-kind evaluation of the Monticello bioshield, assessing long-term adequacy of the structural steel and concrete with exposure to irradiation and thermal effects. The analysis introduced reasonable inputs in place of overly conservative assumptions and considered multiple potential aging mechanisms in order to comprehensively assess future conditions. The results of the evaluation were accepted by the NRC, demonstrating a success path to perform similar evaluations for other sites pursuing LR/SLR. These analyses are unique on a case-by-case basis, as each plant’s design, construction, and operational history will result in different regions and/or components being included in the evaluation.
References
- U.S. NRC Report NUREG-2192, “Standard Review Plan for Review of Subsequent License Renewal Applications for Nuclear Power Plants,” July 2017.
- U.S. NRC Report NUREG-1509, “Radiation Effects on Reactor Pressure Vessel Supports,” May 1996.
News and Views, Volume 55 | UPDATE: Encoded Phased Array Ultrasonic Examination Services for Cast Austenitic Stainless Steel (CASS) Piping Welds in Pressurized Water Reactor (PWR) Coolant Systems
/in Company News, Jason Van Velsor, John Hayden, News and Views, Nuclear Asset Integrity, Nuclear Energy/by Structural IntegrityBy: John Hayden and Jason Van Velsor
Our initial article on this topic in News & Views, Volume 531 describes the challenges imposed by cast austenitic stainless steel (CASS) materials and the development of our CASS UT Examination solution. At the time of the prior article’s publication, SI was also conducting examinations of numerous CASS piping specimens. This article provides details of both that performance demonstration and the results of those examinations.
TYPICAL CASS PIPING WELD LOCATIONS IN PWR REACTOR COOLANT SYSTEMS
Figure 1 illustrates the presence of CASS piping components, both statically and centrifugally cast, in the primary Reactor Coolant Systems of many U.S. PWR plants. Other PWR plant designs also contain CASS components, albeit in fewer locations and only in the form of short spool piece segments, usually for reactor coolant pumps and safety injection system safe ends.
Figure 1. Locations of CASS piping components, both statically and centrifugally cast, in primary Reactor Coolant Systems of many U.S. PWR plants
REGULATORY BASIS FOR CASS EXAMINATION CAPABILITY
ASME Section XI Code Case N-824, which was approved by the NRC in 2019, provides specific direction and requirements for ultrasonic examination of welds joining CASS components. N-824 was incorporated into Section, XI, Appendix II, Supplement 2 in the 2015 Code edition. The NRC has stated (10CFR50.55a, 07/18/2017) that with use of the aforementioned N-824 methodology “Licensees will be able to take full credit for completion of the § 50.55a required in-service volumetric inspection of welds involving CASS components.” SI’s procedure development and demonstration were therefore based on these requirements.
ULTRASONIC TECHNIQUE PERFORMANCE DEMONSTRATION
Though not required by the ASME Code, SI conducted a performance demonstration of our CASS UT system at our facility in Huntersville, NC. Using CASS piping system specimens on loan from the EPRI NDE Center, SI successfully validated our ultrasonic examination system capabilities as follows.
Ultrasonic Procedure – SI’s CASS ultrasonic examination procedure is fully compliant with ASME Section XI Code documents, and NRC-imposed technical approval conditions. The procedure has also been optimized with many insights gained from our laboratory experiences while examining EPRI-owned CASS piping specimens.
Ultrasonic Equipment – The ultrasonic system components required by Code have been designed and fabricated by SI or purchased, including the following:
- Ultrasonic instrumentation capable of functioning over the entire prescribed ranges of examination frequencies. The standard examination frequency range extends from low-frequency, 500 KHz operation for CASS pipe welds > 1.6” Tnom and 1.0 MHz for CASS pipe welds ≤ 1.6” Tnom
- Transducer arrays were employed to meet the physical requirements of frequency and aperture size capable of generating the Code-prescribed wave mode, examination angles, and focal properties.
- An assortment of wedge assemblies were designed and fabricated then mated with transducer arrays to provide effective sound field coupling to the CASS components being examined.
Data encoding options necessary to acquire ultrasonic data given the expected range of component access and surface conditions are available. The encoding options include:
- A fully-automated scanning system capable of driving the relatively large and heavy 500KHz phased array probes. This system was used during our laboratory examinations of CASS piping specimens.
- A manually driven encoding system — a proven, field-worthy tool — which may be employed in locations where fully automated systems cannot be used because of access restrictions.
Examination Personnel – The challenges that exist with the examination of CASS piping welds warrant a comprehensive program of specialized, mandatory training for personnel involved with CASS examinations. This training includes descriptions of coarse grain structures, their effect on the ultrasonic field, the expected ultrasonic response characteristics of metallurgical and flaw reflectors, and the evaluation of CASS component surface conditions.
Additionally, SI’s ultrasonic examination personnel are thoroughly trained and experienced in all elements of encoded phased array ultrasonic data acquisition and analysis in nuclear plants and hold multiple PDI qualifications in both manual and encoded phased array DM weld techniques.
EPRI CASS PIPING SPECIMENS
The EPRI CASS pipe specimens, their outside diameter (OD) and thickness dimensions, and butt weld configurations examined by SI are described below.
12.75″ OD, 1.35″ Tnom SPECIMENS
Three pipe-to-pipe specimens representative of piping found in pressurizer surge and safety injection applications were examined. Each of these specimens had the weld crown ground flush.
Figure 2. Schematic of 12.75” OD, 1.35” Tnom CASS specimens.
Figure 3, Figure 4, and Figure 5 present examples of ultrasonic data images of a flaw detected in a 12.75” OD pipe-to-pipe tapered specimen.
Figure 3. Representative ultrasonic C-Scan data image from 12.75” OD, 1.35” Tnom specimen.
The C-Scan is a 2-D view of ultrasonic data displayed as a top (or plan) view of the specimen. The horizontal axis is along the pipe circumference, and the vertical axis is along the pipe axis or length.
Figure 4. Representative ultrasonic B-Scan data image from 12.75” OD, 1.35” Tnom specimen.
The B-Scan is a 2-D view of ultrasonic data displayed as a side view of the specimen. The angular projection of the data is displayed along the examination angle. The horizontal axis is along the pipe axis, and the vertical axis is along the pipe thickness.
Figure 5. Representative ultrasonic D-Scan data image from 12.75” OD, 1.35” Tnom specimen.
The D-Scan is a 2-D view of ultrasonic data displayed as an end view of the specimen. The horizontal axis represents the pipe circumference, and the vertical axis is along the pipe thickness.
28″ OD, 2.0″ Tnom SPECIMENS
Four pipe-to-pipe specimens representative of piping found in reactor coolant loops were examined. Each of these specimens had the weld crown intact and left in place.
Figure 6. Schematic of 28” OD, 2.0” Tnom CASS specimens.
Figure 7, Figure 8, and Figure 9 present examples of ultrasonic data images of a flaw detected in a 28” OD pipe-to-pipe tapered specimen.
Figure 7. Representative ultrasonic C-Scan data image from 28” OD, 2.0” Tnom specimen.
The C-Scan is a 2-D view of ultrasonic data displayed as a top (or plan) view of the specimen. The horizontal axis is along the pipe circumference, and the vertical axis is along the pipe axis or length.
Note the ability of our UT data acquisition equipment and data analysis techniques to resolve, discriminate, and identify inside surface geometric conditions (weld root and pipe counterbore), along with detecting and sizing the flaw indication. Also, note the excellent signal-to-noise ratio achieved.
Figure 8. Representative ultrasonic B-Scan data image from 28” OD, 2.0” Tnom specimen.
The B-Scan is a 2-D view of ultrasonic data displayed as a side view of the specimen. The angular projection of the data is displayed along the examination angle. The horizontal axis is along the pipe axis or length. The vertical axis is along the pipe thickness.
Figure 9. Representative ultrasonic D-Scan data image from 28” OD, 2.0” Tnom specimen.
The D-Scan is a 2-D view of ultrasonic data displayed as an end view of the specimen. The horizontal axis is along the pipe circumference, and the vertical axis is along the pipe thickness.
28″ to 29″ OD, 2.0″ to 2.5″ Tnom TAPERED WELD SPECIMENS
Four pipe-to-pipe specimens, with tapered weld surfaces representative of piping found in reactor coolant loops were examined.
Figure 10. Schematic of 28” to 29” OD, 2.0” to 2.5” Tnom CASS specimens.
Figures 11, 12, and 13 present examples of ultrasonic data images of a flaw detected in a 28” OD to 29” OD pipe-to-pipe tapered specimen.
Figure 11. Representative ultrasonic C-Scan of a 28” to 29” OD, 2.0” to 2.5” Tnom pipe-to-pipe, with tapered weld surfaces.
The C-Scan is a 2-D view of ultrasonic data displayed as a top (or plan) view of the specimen. The horizontal axis is along the pipe circumference, and the vertical axis is along the pipe axis, or length.
Figure 12. Representative ultrasonic B-Scan of a 28” to 29” OD, 2.0” to 2.5” Tnom pipe-to-pipe, with tapered weld surfaces.
The B-Scan is a 2-D view of ultrasonic data displayed as a side view of the specimen. The angular projection of the data is displayed along the examination angle. The horizontal axis is along the pipe axis or length. The vertical axis is along the pipe thickness.
Figure 13. Representative ultrasonic D-Scan of a 28” to 29” OD, 2.0” to 2.5” Tnom pipe-to-pipe, with tapered weld surfaces.
The D-Scan is a 2-D view of ultrasonic data displayed as an end view of the specimen. The horizontal axis is along the pipe circumference, and the vertical axis is along the pipe thickness.
SUMMARY OF DATA ANALYSIS RESULTS
Documentation was provided for each EPRI specimen, which contains flaw location, length, and through-wall size to permit the comparison of UT data acquisition and analysis processes to actual flaw conditions.
All of the 23 circumferential flaws in the eleven EPRI specimens were detected. The ultrasonic examination and data analysis techniques achieved flaw location and length sizing RMS errors, which are within acceptance standards of the following ASME Section XI, Appendix VIII Qualification Supplements:
- Supplement 2, Qualification Requirements for Wrought Austenitic Stainless Steel Piping
- Supplement 10, Qualification Requirements for Dissimilar Metal Piping
Excellent signal-to-noise ratios were observed for all detected flaws.
For all flaws, the measured length achieved sizing RMS errors within the acceptance standards of the above Appendix VIII supplements.
For specimens with welds ground flush and for all specimens with sufficient access to interrogate the entire through-wall extent of flaws, SI’s technique achieved through-wall sizing RMS errors within the acceptance standards of the above Appendix VIII supplements.
To be clear, the examination of the EPRI CASS specimens does not meet the rigor of Appendix VIII, Supplement 9 qualification because the industry’s (PDI Program) for CASS piping welds is still in preparation. The comparison to Appendix VIII acceptance standards is provided solely as a means to describe the achieved flaw detection and sizing capabilities in CASS material in terms of already established PDI qualifications. Ongoing examination of additional CASS specimens will strengthen already existing ultrasonic examination capabilities and experience.
CONCLUSIONS
The CASS piping welds in many PWR plants provide numerous and complicated challenges to their effective ultrasonic examinations. Most, if not all, CASS RCS piping welds have not been subjected to a meaningful and effective volumetric examination since radiography was conducted during plant construction. SI’s newly-demonstrated ultrasonic examination procedure for CASS delivers a demonstrated, Code-compliant, meaningful, and effective solution that provides full credit for completion of in-service volumetric inspection per § 50.55a.
References
- News and Views, Volume 53, October 2023, “Encoded Phased Array Ultrasonic Examination Services for CASS Piping Welds In PWR Reactor Coolant Systems”
- ASME Section XI Code Case N-824, “Ultrasonic Examination of Cast Austenitic Piping Welds from the Outside Surface”
- ASME B&PV Code, Section XI, 2015 Edition and later editions
News and Views, Volume 54 | Structural Integrity Supports Pipeline Research Council International’s Hard Spot Project
/in Company News, News and Views, Oil and Gas Pipeline, Scott Riccardella, Steven Osgood/by Structural IntegrityBy Scott Riccardella and Steven Osgood
Structural Integrity is pleased to be working with PRCI to improve ILI performance, provide industry insight regarding prioritizing hard spots, and determine the optimal repair methodologies.
SI’s Pipeline Integrity Compliance Solutions (PICS) group has been implementing a highly strategic project from the Pipeline Research Council International (PRCI) focused on enhancing industry capabilities to detect and assess hard spot anomalies in gas transmission and hazardous liquid pipelines.
PRCI reviewed proposals from several highly qualified firms to support this project. Ultimately, SI was selected to provide support based on a combination of our expertise and integrated proposal, which demonstrated capabilities in field assessment, engineering analysis, and a reputation for providing synchronized follow-up. Being part of this PRCI project reinforces SI’s dedication to helping improve pipeline integrity and assessment practices and further position SI as an expert consulting partner for supporting pipeline operators’ fracture mechanics and in-line inspection (ILI) needs.
About the Project
Hard spots, or localized areas with elevated hardness within the pipe body, were believed to form during manufacturing. Hard spots are prevalent in piping produced by certain manufacturers and/or within certain vintages. They are believed to be attributed to inadequate quality control in the steelmaking, pipe-rolling, and welding processes. Over time, when in specific environmental conditions, cracking can initiate in the hard spots, creating a significant hazard. PRCI issued an RFP focused on evaluating and enhancing ILI tool technology and complementary analytical capabilities to reliably detect, size, and characterize the threat to integrity caused by hard spots.
Project Objective and Details
The project objective is to help the industry better understand ILI performance for more accurate detection and characterization of hard spots, providing targeted feedback, and developing insights to help improve ILI performance and prioritize ILI results.
ILI Performance Evaluation Study
The project’s main task is to evaluate the performance of various ILI technologies and service providers in identifying and characterizing hard spot defects. Testing is performed at the PRCI Technology Development Center (TDC) with pipeline samples (with various hard spot features) removed from service and configured in a test string for pull-through testing from several participating service providers. SI has characterized these samples using advanced NDE methodologies to establish reference data that will be used for determining the probability of detection (POD), probability of identification (POI), sizing accuracy, hardness estimation accuracy, and location accuracy. Individual performance reports will be provided as feedback to the participating ILI service providers to facilitate improving and advancing ILI technologies for hard spot detection and characterization.
Developing the Repair/Response Criteria
Following this testing, SI will complete additional analysis and modeling of the ILI Reported Values versus measured dimensions and hardness values for associated error. SI will also perform modeling to develop statistical correlations (with associated uncertainties) for estimating the Peak Hardness & Hard Spot Length from ILI Reported Values. Data will be analyzed in the context of historical failures and regulatory definitions of a hard spot. SI will develop an assessment methodology to evaluate hard spot criticality with a recommended response criterion (feature prioritization scheme) based on feature severity (length, hardness) and relative safety margin (Predicted Failure Pressure / MAOP).
“This project helps advance a critical initiative for PRCI, helping improve ILI capabilities to address a key threat to pipeline integrity. We are grateful to be partnering with Structural Integrity to develop and deploy this knowledge to our members.”
Jim Wayman – Program Manager Integrity and Inspection – PRCI
Evaluation & Recommendation of the Repair Methodology
SI is also working to complete research on different material properties and repair methodologies to determine the suitability of repairs. As part of this task, SI will complete a benchtop study using finite element analysis (FEA) to study the effectiveness of each repair approach (composites and Type A sleeves) leveraging the fitness for service (FFS) methodology detailed in the prior task (Repair/Response Criteria).
Structural Integrity Associates Acquired by MidOcean Partners
/in Company News/by Structural IntegritySAN JOSE, CA – August 15, 2024 – SI Solutions today announced their acquisition by MidOcean Partners. The transaction includes SI Solutions and all its affiliate companies: Structural Integrity Associates, C2C Technical Services, and SC Solutions. The full press release with additional details follows below.
NEW YORK – August 15, 2024 – MidOcean Partners (“MidOcean”), a premier New York-based alternative asset manager specializing in middle-market private equity, structured capital, and alternative credit investments, today announced the acquisition of SI Solutions (“SI” or the “Company”), a leading provider of engineering, testing, inspection, compliance and maintenance services, digital solutions, and expert consulting for power and critical infrastructure end markets. Terms of the transaction were not disclosed.
With more than 450 employees, SI provides technical expertise and services to enable the reliability and resiliency of the U.S. power markets, safety and regulatory compliance of critical assets, and continued expansion of public and private infrastructure in the U.S. and abroad. The Company will continue to be led by Chief Executive Officer Mark Marano, who previously served as COO of Westinghouse Electrical Company and has deep operating experience in the utility and critical infrastructure markets. In connection with the acquisition, SI’s management team, employee shareholders, and prior investor Jumana Capital have reinvested in the business.
Elias Dokas, Managing Director at MidOcean, said, “SI is a proven industry leader with a stellar track record of serving the power and critical infrastructure markets and delivering superior engineering and specialty services to its clients. The Company has experienced tremendous growth to date and we see numerous opportunities for further growth through organic initiatives and strategic acquisitions, including expanding its service offerings and entering new markets. We look forward to working closely with the SI leadership team to deepen the Company’s relationships with its existing clients and build its market position.”
Brian Finnie, Principal at MidOcean, added, “We are thrilled to be partnering with SI. We believe the combination of SI’s expertise and longstanding client relationships with MidOcean’s utility and infrastructure services experience and dedicated team of operating experts will position the Company for continued growth and success.”
Mr. Marano concluded, “This partnership with MidOcean is the next step in the evolution of the SI Solutions platform, and I’m excited about the future of the company. We will continue our mission to power the future of critical infrastructure, leveraging our highly skilled employees and our drive for innovation to deliver unparalleled value to our clients. MidOcean provides us with the additional capabilities and experience to further our mutual goals to serve our industries.”
The acquisition of SI marks MidOcean’s fourth investment in the engineering and critical infrastructure sector. MidOcean previously invested in, and has since successfully exited, System One and The Planet Group. The firm also recently announced a preferred equity investment through its structured capital initiative in GridHawk Holdings, a premier provider of damage prevention services for critical utility infrastructure across the U.S.
MidOcean was represented in the transaction by Gibson, Dunn & Crutcher LLP as legal advisor. Stifel, Nicolaus & Company, Inc. served as exclusive financial advisor to SI. Locke Lord LLP acted as legal advisor to SI and Jumana Capital.
About MidOcean Partners
MidOcean Partners is a premier New York-based alternative asset manager specializing in middle-market private equity, structured capital, and alternative credit investments. Since its inception in 2003, MidOcean Private Equity has targeted investments in high-quality middle-market companies in the consumer and business services sectors. MidOcean Credit Partners was launched in 2009 and currently manages a series of alternative credit strategies, collateralized loan obligations (CLOs), and customized separately managed accounts. For more information, please visit: https://www.midoceanpartners.com/
MidOcean Investor Relations Contact:
Investorrelations@midoceanpartners.com
MidOcean Media:
Amanda Shpiner/Grace Cartwright
Gasthalter & Co.
(212) 257-4170
midocean@gasthalter.com
About SI Solutions
SI Solutions provides technical expertise and services to enable the reliability and resiliency of power markets, safety and regulatory compliance of critical assets, and continued expansion of public and private infrastructure in the U.S. and abroad. The company is a leading provider of engineering, testing, inspection, compliance and maintenance services, digital solutions, and other consulting and advisement activities. For more information, please visit: https://www.sisolutions.com/
Media Contact:
Christopher Sydor
SI Solutions
704-977-1361
info@sisolutions.com
SIGN UP FOR OUR NEWSLETTER
*Join the conversation. Sign up to receive emails, events, and latest information!
1-877-4SI-POWER
(1-877-474-7693)